Solutions pour l'excellence opérationnelle
Un écosystème digital dédié à la performance industrielle
Vous permettre de suivre et d’anticiper le cycle de vie de vos machines, à travers des données pertinentes est notre rôle au quotidien. Notre engagement : contribuer à construire une usine du future plus fiable et plus efficace.
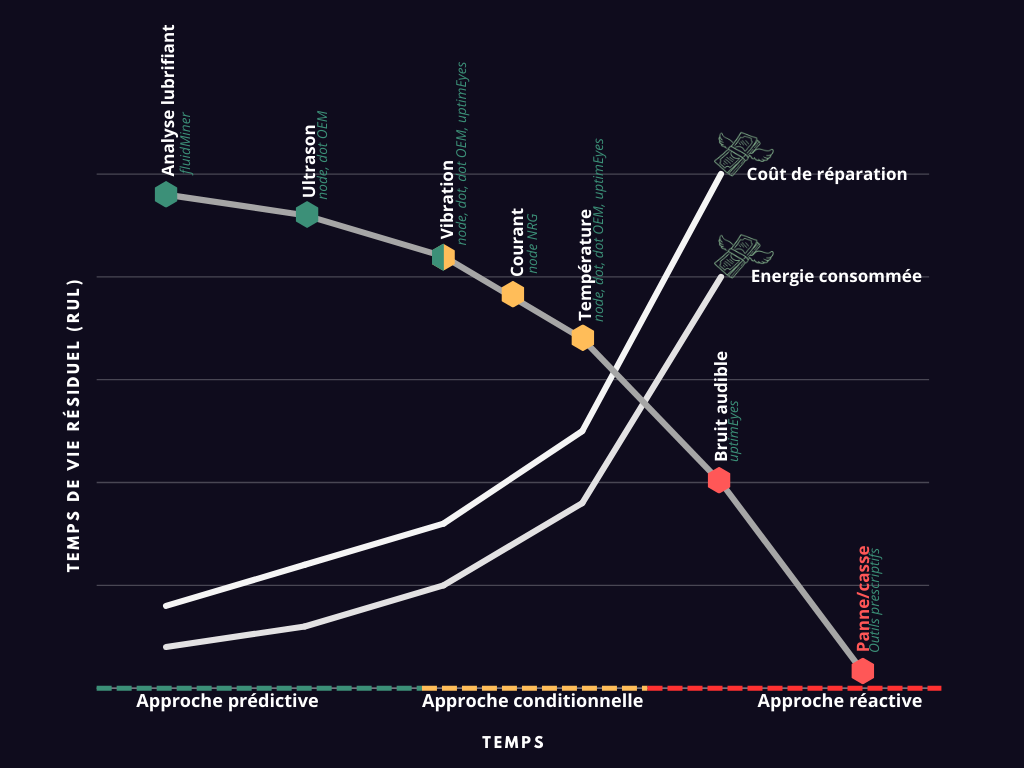
Nous sommes
catalyseurs de leur
performance industrielle.
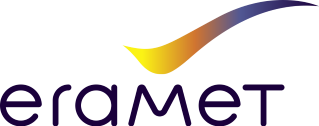
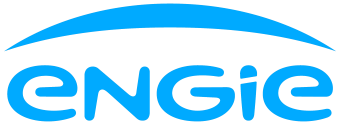

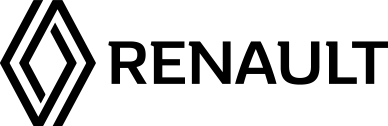
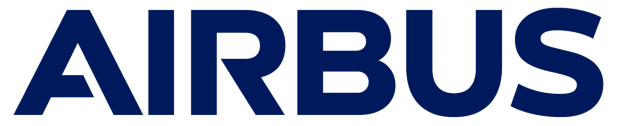

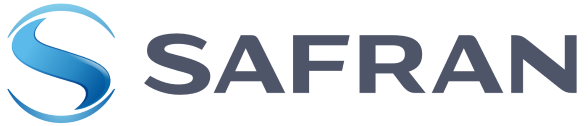